Guide rollers for use in hot rolling mills for long products are exposed to extreme conditions like heat of approx. 1000°C, scale contaminated cooling water, and high rates of revolutions per minute. The rollers are also in direct contact with the hot metal which means extreme abrasive conditions. We supply the rollers with steel material, TiC material and tungsten carbide material according to the different requirement.
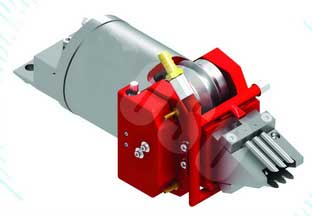
The slitting technology as applied to continuous bar mills enables the production of two or more strands from one billet. Depending on plant configuration the slitting process can be adapted to rolling mills with a minimum of four final stands in continuous installation.
The process gives the following profits:
- Substantial increase in production rates
- Reduction in the number of rolling stands
- Reduction in operation costs
The slit rolling process differs from conventional continuous rolling by the use of special roll passes and guides to prepare, shape and longitudinally separate the incoming billet into two or more individual strands for further rolling into the finished size.
In principal this process is achieved as follows:
- Reducing the billet conventionally through the roughing and intermediate rolling mill to produce an acceptable section for the first special shaping pass at the forming stand.
- Precise guidance of this stock to the forming stand where it is reduced and shaped to form a symmetrical "forming section“.
- Further close guidance and control of the "dog bone“ through the separating stand, were the stock is reduced and shaped into a "slit pass“, designed to be easily separated
- into two equal sections of false round.
- A special guide on the delivery side of the separating stand ensures a clean slitting of the bar and now delivers multiple strand of equal sections to their respective finishing lines.
For the particular demands for guiding of flat and profiled sections can provide our customers with a complete line of roller guides. The design of our line of roller guides is based on our long experience in the field of guiding of profiles and roller guides in general. It means that they are designed with focus on strength and precision and in a user-friendly environment.
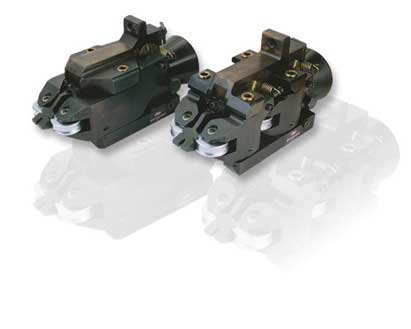
The design of roller guides for high speed applications, such as in wire rod mills, requires certain characteristics in order to fulfil the high demands in high speed rolling.
This in respect of precise setting means close tolerance finish of all parts. Much attention has to be paid to the bearing arrangement in order to withstand the extreme high-speed requirements.
The design of the high speed roller guides where based on the following factors:
- Simple design and easy adjustment.
- Minimised and standardised components.
- Stainless steel material in order to withstand the severe environment in a WRB
- The roller bearings must permit quick acceleration to very high rolling speeds.
- The distance between guide roller and work rolls must be as short as possible (in cases where no nosepiece is used).
- The entry guide halves should be flushed with cooling water in order to keep them free of scale.